Timber frame building
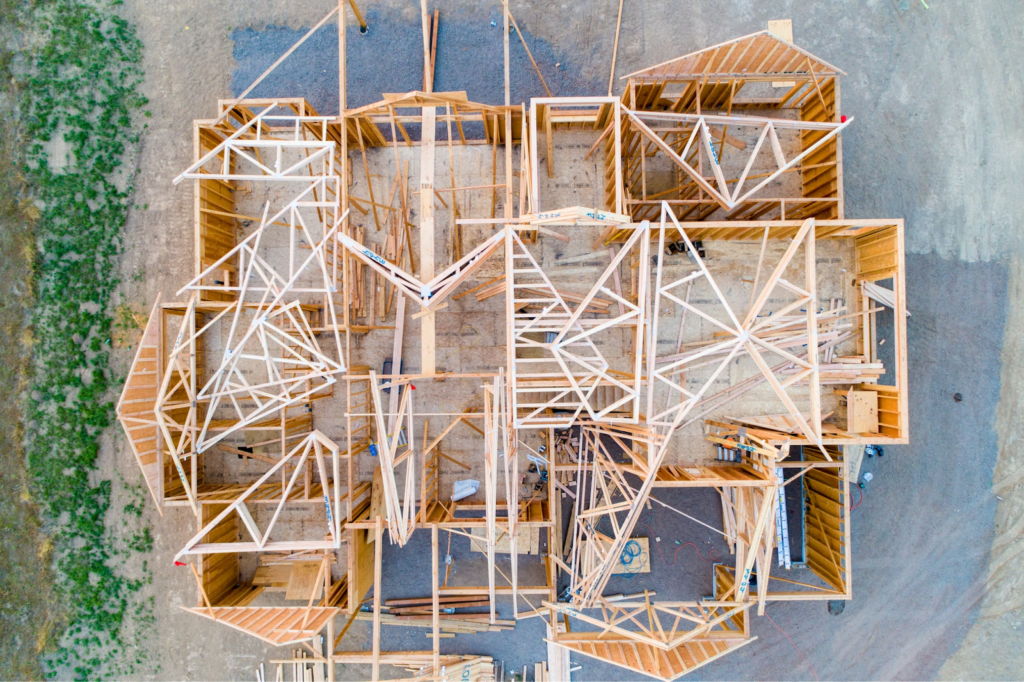
In the realm of construction, the legacy of timber frame building stands as a testament to the harmonious marriage of tradition with cutting-edge innovation. Long before concrete and steel became the dominant materials in construction, wood, in its purest and most refined form, has been moulding the skylines and landscapes of civilisations.
However, as the industry progresses, the details of timber frame construction are also evolving. In this article, we delve deep into timber frame construction details, exploring the infinite possibilities it holds for the future. Whether you’re an architect, a homeowner, or simply a lover of elegant design, there’s a world within timber framing that beckons your exploration.
How are timber frame houses built?
1. Setting the Groundwork for Timber Frame Buildings: Approximately 2-4 weeks
While your timber frame house package is under production, it’s crucial to get started with the foundational work. Generally, two weeks should suffice for foundation work, but the exact duration can fluctuate based on the specific plot.
During the preliminary phase, the building control representative will guide you through potential issues such as encroaching tree roots or unstable soil conditions.
The trench fill technique is a common starting point for most projects. This is suited for firm grounds like clay and chalk, as trench walls play a pivotal role in providing stability. It’s a cost-effective method, eliminating brickwork beneath the soil level.
However, for unconventional plot designs or less firm grounds, strip foundations could be your go-to. This approach distributes the building’s weight over a larger expanse, ensuring stability for trickier plots.
2. Assembling the Frame: Roughly 3-4 weeks
Timber frame buildings typically comprise timber stud walls stabilised with OSB or plywood. The panels are considered ‘closed’ once they’re insulated. Depending on the design specifics, your timber frame package could arrive either open or closed. An advantage of the closed design is the pre-installed insulation.
Erecting the pre-made frame is usually quick, but you should allocate two to four weeks in your schedule to account for complexities and unforeseen weather conditions. If the design incorporates a room within the roof, cassette roofing might be integrated.
Ensure the building is completely shielded from the elements before progressing. After weatherproofing, the final external cladding can be added.
3. Initial Installations: About 3-4 months
Upon ensuring a watertight structure, it’s time for the installation of utilities. Coordinating with skilled tradespeople can expedite the process. The primary installations comprise electrical circuits, water and gas pipelines, and HVAC systems. Once these are in place, the next step involves setting up plasterboard fixtures and other structural elements. Professional assistance is advisable during this phase.
4. Secondary Installations: A few weeks
This phase transforms the building structure into a welcoming home. From setting up light fixtures to designing the kitchen and bathroom, every detail falls into place. Depending on various factors, this phase might span a few weeks.
5. Functional Assessments: About a week
Ensure the building undergoes necessary airtightness and sound checks. Some suppliers, like Scotframe, might include these services in their packages.
6. Fine-Tuning and Adjustments: Several weeks
Examine your timber frame construction for any discrepancies or finishing issues. Addressing these ‘snags’ ensures your house stands strong and beautiful for years to come.
7. External Embellishments: A few weeks
This phase breathes life into the exterior of your home. The duration can vary based on the aesthetic goals and intricacies involved.
8. Wrapping Up
Once everything is in place, get the necessary certifications and approvals to move into your timber frame home. Transition your insurance to a homeowner’s policy and ensure you’re aligned with the regulations specific to your region, whether it’s England or Scotland.
Is constructing timber frame buildings more cost-effective?
Given the myriad of factors at play. The final price tag of a timber frame construction can be influenced by various aspects. Factors such as design intricacies, intricate roofing designs, elevated ceilings, open floor plans, and specialty windows can drive up costs. Furthermore, accessibility, the ratio between floor and wall areas, and the specific timber frame construction details and systems chosen play a role in the overall expenditure.
Timber frame buildings range in price extensively. For instance, there are lavish two-storey timber frame homes sprawled across expansive plots priced over £850,000. On the flip side, one-bedroom timber frame self-builds can be created on a tighter budget, sometimes under £80,000 according to HomeBuilding.
When breaking down expenses, the superstructure of a timber frame build usually accounts for approximately 25% to 30% of the entire budget according to HomeBuilding. When juxtaposed with methods like brick and block, the initial costs of an open-panel garden room or building align similarly. However, closed-panel systems might come with a heftier price, especially when considering enhanced performance and additional features.
Understanding the Pros and Cons of timber frame building
When evaluating construction systems like timber frame building, it’s crucial to weigh the advantages against the disadvantages. Timber frame construction, a popular choice for structures like garden rooms and other timber frame buildings, is no exception. Here’s a detailed look at the timber frame construction details highlighting its benefits and challenges:
Benefits of Timber Frame Construction:
1. Eco-Friendly: Using responsibly-sourced timber promotes sustainable construction, ensuring that timber frame buildings leave a smaller ecological footprint.
2. Efficiency in Material Use: Timber frame construction typically results in less material wastage, making it a more resource-efficient choice.
3. Speed: Timber frame structures can be constructed about 30% faster compared to traditional block and brick methods according to HomeBuilding.
4. Lightweight: The lighter weight of timber frames often translates to simpler and cost-effective foundation requirements.
5. Weather-Resilient Construction: Unlike block builds, timber frame constructions can proceed even during adverse weather conditions without significant delays.
6. Precision: Timber frames are manufactured with high precision, reducing the scope for on-site errors and ensuring rooms are perfectly level and square.
7. Less Dependency on Wet Trades: Reducing reliance on wet trades not only addresses their limited availability but also curtails mess on construction sites.
Challenges of Timber Frame Construction:
1. Groundwork Precision: Given that timber frames are precision-made, any deviation in the groundwork can pose challenges, sometimes hard to rectify.
2. Varied Panel Weights: Some timber frame panels can be considerably heavier, necessitating cranes for positioning, which might complicate site access.
3. Heat Fluctuations: Timber frame buildings might experience more pronounced heat fluctuations due to their lesser mass compared to block-built homes. However, this is counterbalanced by the fact that timber frame construction seamlessly integrates with good insulation practices.
4. Cost Considerations: Per square meter, a timber frame might be pricier than block and brick. However, the accelerated construction pace can offset these costs, potentially making it more economical in the long run.
5. Payment Terms: Many timber frame companies seek substantial deposits, occasionally the full amount, before initiating construction, posing cash flow challenges for certain self-builders.
Comparison of Stick Built and Pre-manufactured Construction
Understanding the distinctions between stick built and pre-manufactured timber frame construction is crucial when discussing timber frame buildings.
Stick Built Timber Frame Construction
Stick built timber frame building is a method where each piece, or “stick”, is assembled one by one on the construction site. In essence, stick built frames should encompass all the mentioned timber frame construction details, enabling them to function similarly to other timber frames.
However, there are challenges with this approach. Stick built timber frame buildings are often assembled based on traditional customs rather than specific engineered designs. This makes the process slower and less efficient. Without the capacity for rigorous testing during the construction process, the energy efficiency, structural integrity, and fire resistance of these frames remain largely unverified. This lack of assurance causes many warranty providers and financial institutions to view this method with caution.
Pre-manufactured Timber Frame Construction
In contrast, contemporary timber frame buildings and extensions, such as a garden room, leverage precision-engineered panels produced off-site. These panels often come with the necessary insulation and membranes to guarantee the required performance.
These wall panels, tailored to the specifications of a project, form an integral part of the building’s structure. Emphasis is often on creating large, efficient panels that streamline the building process.
The advantages of pre-manufactured timber frame construction lie in its controlled, off-site manufacturing environment. This setup ensures a consistent quality. Due to their standardised design, these panels undergo thorough testing, verifying their performance capabilities. For instance, leading manufacturers conduct tests on loadbearing fire resistance. These tests confirm the timber frame’s stability during a fire and its compliance with Building Regulation requirements.
Deciding on the Right Timber Frame Construction Details
When contemplating the type of timber frame house to opt for, it’s essential to consider regulations and warranty needs. While both methods have their merits, only pre-manufactured panels that undergo rigorous testing guarantee the necessary certification for building regulations compliance, ensuring peace of mind for both builders and warranty providers.
Choosing Between Open and Closed Panel Timber Frame Systems:
Open Panels: These are pre-made, making them ready for the installation of external joinery such as doors and windows. Delivered with the required flooring components and roof trusses, work can kick off on both the interior and exterior immediately after the timber frame construction team wraps up.
Closed Panels: These come to the construction site with pre-installed insulation. Other components like external cladding, windows, and doors might also be pre-fixed. Moreover, they can come equipped with pre-installed electrical and plumbing systems, or a service cavity for those who are yet to finalise their utility plans. Predominantly supplied by German turnkey home producers, closed panels can significantly speed up construction timelines. However, given their weight, cranes are indispensable for their installation.
In essence, timber frame panels can either be “open” or “closed,” depending on the builder’s preference and the project’s requirements.
Understanding Structural Insulated Panel Construction:
Often dubbed as “timber frame without the timber,” the robustness of these panels stems from insulation sandwiched between an internal and external board layer, forming a highly rigid and well-insulated structure. These panels, manufactured in factories, come with designated spaces for doors and windows. Once delivered to the site, they, along with the flooring components and roof trusses, form the primary structure of the house within mere days. One of its most commendable advantages is its rapid construction pace, even in unfavourable weather conditions, ensuring efficiency and minimal downtime.
With the right timber frame construction details, whether you’re considering a garden room or other timber frame buildings, making an informed choice is crucial for the success and longevity of the structure.
Discover Timber frame buildings With Pasquill
Don’t just build; craft a legacy with Pasquill’s expert timber frame solutions. Dive deep into the world of timber frame construction and let us guide you every step of the way.
From design nuances to structural details, Pasquill stands at the forefront of timber innovation. Whether you’re envisioning a bespoke garden room or an expansive timber frame building, our expertise ensures precision, durability, and beauty.
Don’t wait; transform your architectural dreams into timber realities with Pasquill. Reach out today and embrace the future of construction.