Housebuilder Insight: Debunking Off-site myths
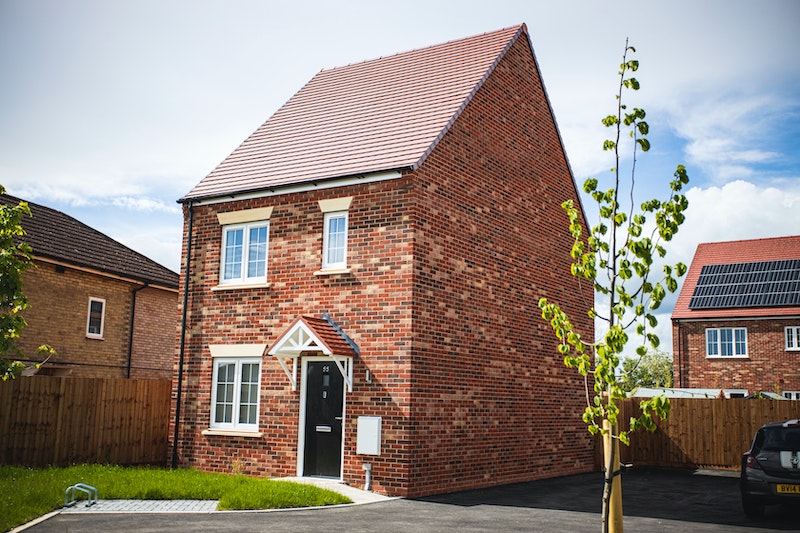
The construction industry is always evolving and developing. With new technologies, methods and practices being implemented on a regular basis, companies within the sector are always looking for the ‘next best thing’ to help them going forward.
It’s no secret that we’re big fans of off-site manufacturing (OSM), and we’re always keen to show how it can help housebuilders and designers to improve their builds. However, do others in the industry really know what the true benefits are? And if so, are they really using it to its greatest potential?
With this in mind, we decided to find out as part of the second instalment of our housebuilder insight series. We conducted research into what the perceived ‘myths’ surrounding OSM actually were, and learnt several interesting things about the priorities of housebuilders when dealing with OSM.
What are the benefits of OSM?
We asked 100 housebuilders what their perceived benefits of using OSM were to their organisation. Their answers showed that many of the assumed benefits of OSM were not considered to be huge priorities.
Speeding up construction
Speed came in as the top OSM benefit for 75% of respondents. And they’re right to say so: this approach takes the majority of construction away from the building site, without the need to battle delays such as poor weather or staff shortages. Plus, the use of larger pre-assembled components simply makes construction itself a quicker process compared to traditional building methods.
With so many housebuilders under pressure to build more homes faster, it’s no surprise that speed ranks the highest. Read more about how we supplied 60 floor cassettes to an MMC trial development in Norwich that experienced a 35% timesaving.
Cost savings
Another factor which rated very highly in our survey was the cost savings that OSM could generate. Just under half (44%) agreed that taking their projects off-site can help with the financial bottom line – both in terms of the construction process and the lifetime of the build.
With an increasingly uncertain economic situation ahead this is truer than ever. Ultimately, homes still must be built, it’s about finding the most affordable way to achieve that without sacrificing quality. Request a quote to find out how much we could save you on your next project.
Reducing the skills gap
With the skills shortage being one of the biggest issues facing the industry today, it was surprising to see only 15% of housebuilder respondents cite this as a reason for choosing the method. A mix of factors, such as fewer young people learning the vocational trade while more and more experienced builders are due to retire, means this problem is only going to become more apparent.
Thankfully, OSM can tackle this issue directly, with the need for many fewer tradespeople on-site. Plus, we’re doing our bit to create a pipeline of talent within the digital construction industry with a Junior Designer Programme. This aims to equip the next generation with the skills needed to successfully implement OSM across the industry.
Make sustainability a priority
It’s essential that we build greener homes. The construction industry is traditionally one of the greatest global offenders of carbon emissions. Thankfully, newer and cleaner building technologies, such as off-site timber frame components, are helping to create a better future. Alas, only a handful of housebuilders cited this as their main reason for choosing OSM – however we’re confident that this will change in the future now that sustainability is a key part of the sector’s agenda.
Making the switch to off-site
Ultimately, one of the biggest stats that surprised us was that almost 1 in 5 of housebuilders who answered said that they still don’t use OSM. With so many benefits available, alongside regulations such as the Future Homes Standard and the Affordable Homes Programme, there truly has never been a better time to venture into these new building methods.
Through our connections within the Saint-Gobain Off-Site Solutions group, we are innovating the use of timber-engineered timber frame components to tackle the issues affecting the sector. And now, with some of the ‘myths’ surrounding OSM debunked, we hope that even more within the construction industry can see the benefits of using the approach in the future.
Speak to us today to discover how we can help you on your next project.