Floor Joist Timber UK Regulations: NHBC
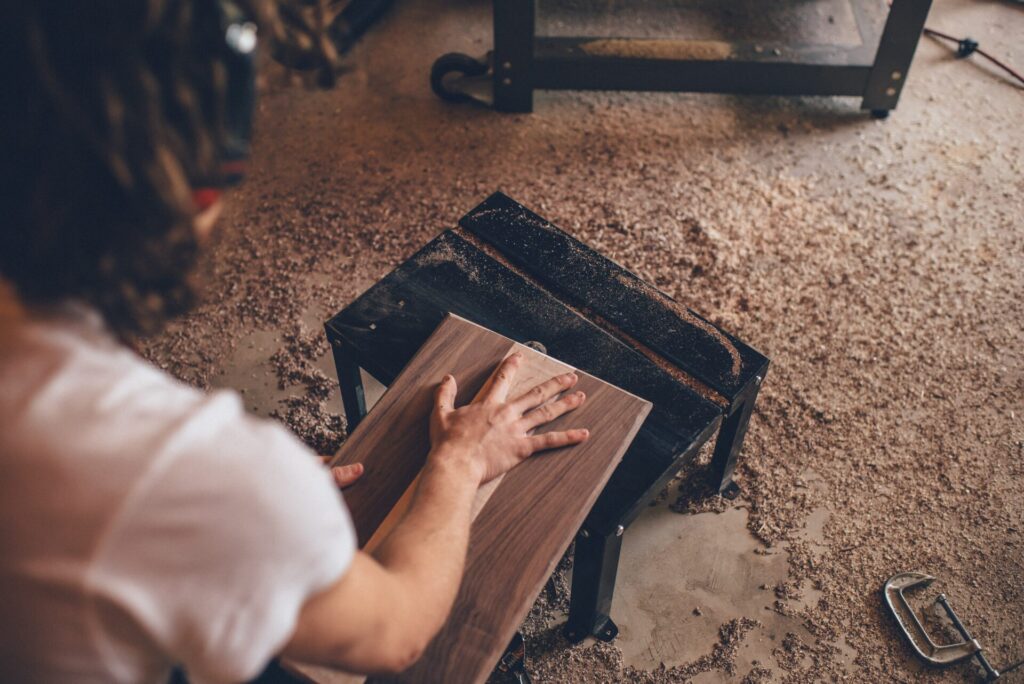
Significant changes in standards in 2023 are set to reshape the landscape of home construction. This article will delve into these transformative developments and show how Pasquill has adapted to align with these revised benchmarks.
The NHBC Standards, renowned for defining the technical prerequisites and performance criteria for newly registered homes, will be explored in the context of these dynamic changes, along with insights on how these benchmarks will be met.
What are the new NHBC standards for timber floor joists?
The latest edition of the Standards introduces several significant technical updates:
1. In Chapter 5.3, you’ll find new inspection chamber recommendations and additional guidance on designing surface soakaways for gardens measuring less than 100m2.
2. Chapter 5.4 now includes guidance on safeguarding below-ground structures against water infiltration, aligning with the standards outlined in BS 8102:2022.
3. Chapter 6.1 provides fresh insights into the placement of horizontal movement joints for masonry-clad buildings and raises the performance standards for cavity walls.
4. Chapter 6.4 has been updated to encompass revisions related to concrete upper floor design and limits on timber I-joist deflection.
5. Chapter 6.7 now incorporates updated guidance on ensuring windows, doors, and glazing weather tightness.
6. Chapter 7.2 introduces modifications related to underlay and sarking, ventilation, vapour control and insulation, battens, fixing of tiles and slates, valleys and concealed gutters, traditional roof arrangements, and the protection of trussed rafter roofs, as well as specifying bracing requirements.
7. Chapters 8.1 to 8.3 have been amended to prepare for future carbon reduction requirements, featuring new guidance on heat pump design and specifications, certification requirements, solar thermal systems, and space heating systems.
8. Chapter 9.1 introduces new guidance on applying decorative coatings to steelwork.
9. In Chapter 10.1, you’ll find fresh recommendations on implementing ground gas precautions for integral or attached garages and guidance on supporting single-leaf garage walls up to 200mm in thickness.
Why are the new NHBC standards necessary?
The new NHBC (National House Building Council) standards are of significant importance for multiple reasons:
Safety
The NHBC standards prioritise the safety of new homes. They set specific requirements and guidelines that help ensure that homes are constructed to minimise risks to occupants. This includes regulations related to structural integrity, fire safety, and health and safety during construction.
Quality
The NHBC standards establish quality benchmarks for construction. By adhering to these standards, builders and developers are committed to delivering high-quality homes that meet or exceed industry-recognized criteria. This can result in homes that are more durable, energy-efficient, and comfortable for their occupants.
Energy Efficiency
As environmental concerns continue to grow, the NHBC standards increasingly focus on energy efficiency and sustainability. This is vital for reducing the carbon footprint of new homes and ensuring they meet modern environmental expectations. Compliance with these standards can lead to homes that are more energy-efficient and cost-effective for homeowners.
Long-Term Investment
Homes are often the most significant investments that individuals make. The NHBC standards ensure that the homes built are constructed to last and maintain their value over time. This is particularly important for homeowners who want their investment to hold or appreciate.
Legal and Regulatory Compliance
Many NHBC standards are closely aligned with legal and regulatory requirements. Compliance with these standards helps builders and developers meet their legal obligations, reducing the risk of legal disputes or issues with regulatory authorities.
Consumer Confidence
Homebuyers and homeowners benefit from the NHBC standards as they provide transparency and accountability. When a home is built to NHBC standards, it gives consumers confidence that they are getting a well-constructed, safe, and energy-efficient property.
Resale Value
Homes built to NHBC standards often have a better resale value. Potential buyers are more likely to trust the quality of a home that adheres to recognised industry standards, which can lead to quicker sales and potentially higher selling prices.
Adaptation to Changing Needs
The NHBC standards evolve to adapt to changing societal and technological needs. This means that homes built to these standards are more likely to meet the expectations of modern living, including considerations for technology integration, accessibility, and sustainability.
In summary, the new NHBC standards are essential because they promote safety, quality, energy efficiency, and long-term home investment while ensuring compliance with legal requirements. They give consumers confidence and peace of mind when purchasing or living in a home built to these standards.
NHBC timber floor design
Deflection and vibration limits:
- Should not exceed 0.003 times the span for combined bending and shear, based on total dead and imposed loads.
- Maximum deflection of 14mm with strutting, or 12mm without strutting. “Maximum deflection” refers to instantaneous deflection, not the final deflection.
This applies to all floors supplied from 01/01/2023, excluding those stored, ordered, or designed prior to this date.
Starting 1 July 2023, all new floors must adhere to the new requirements, including Pasquil’s designs.
NHBC has clarified that the requirement extends to attic truss floors, and the 2024 NHBC Standards will reflect this clarification.
Part A. Design
When designing structural timber for solid joists, it’s customary to designate them as strength Class C16 or C24. Tables that outline the permissible clear spans for joists falling under strength Class C16 and C24 can be found in the publication “Span tables for solid timber members in floors, ceilings, and roofs (excluding trussed rafter roofs) for dwellings” by TRADA Technology Ltd, which is reproduced in Appendix 6.4-A.
It’s imperative to adhere to the manufacturer’s guidelines for I-joists and metal web joists. Additionally, consider the following deflection limits, which are based on the total combined dead and imposed loads, factoring in bending and shear: The deflection should not exceed 0.003 times the span, with a maximum deflection of 14mm if strutting is present or 12mm if strutting is absent.
It’s essential to note that I-joists and metal web joists should not be employed when any part of the joist is exposed to external weather conditions.
NHBC timber floor joist sizes
Part B. Joist Dimensions
The dimensions of solid timber joists can be found within the span tables featured in BS 8103-3. In cases where these tables do not provide the necessary information or when dealing with concentrated loads, a qualified Engineer should undertake the design of floor joists, following the guidelines specified in Technical Requirement R5.
It is advisable to use regularised timber for floor joists. The cross-sectional sizes mentioned in the tables in Appendix 6.4-A should be regularised, or ALS or CLS should be to ensure that floors and ceilings achieve a level surface.
As for I-joists, metal web joists should be selected and implemented in strict accordance with the instructions provided by their respective manufacturers.
NHBC timber floor joist spacing
Joists should be positioned with a maximum center-to-center spacing of 600mm.
When determining the layout of joist spacings, it’s essential to provide a gap of 25mm to 75mm between the initial joist and the wall surface. This clearance is valuable for accommodating the installation of utilities and securing floorboards in place.
Support of lightweight partitions
Part D. Support for Lightweight Partitions
In cases where multiple solid timber joists provide support for lightweight, non-loadbearing partitions that run parallel to the joists, it is essential to securely fasten them together, as detailed in the Sitework clause 6.4 – S7.
For I-joists and metal web joists, there are two acceptable methods:
1. Position them at the central location beneath a non-loadbearing partition. Following the manufacturer’s instructions, they can be duplicated or triplicated if necessary.
2. To bear the weight of the non-loadbearing partition, they should be augmented with noggings or bearers connecting to the two adjacent joists. Unless otherwise specified in the design, these noggings should measure no less than 38 x 90mm, placed at intervals of 600mm, and securely affixed with metal clips. The sole plate of the non-loadbearing partition should also be fastened to these noggings.
Support of masonry partitions
Part E. Masonry Partition Support
When it is not feasible to construct first-floor masonry partitions directly above ground-floor masonry walls, it is imperative to include steel or reinforced concrete beams in the design to provide the necessary support for the partition. This precaution is essential to mitigate potential issues related to timber beams, such as shrinkage and long-term deflection.
Supporting masonry partitions on joists is generally only acceptable if executed under an Engineer’s guidance, adhering to the specifications outlined in Technical Requirement R5.
Heavy loads
Part F. Handling Heavy Loads
To accommodate heavy loads, the design must include bearers or extra joists. When I-joists and metal web joists are employed, please consult the manufacturer’s provided details for specific guidance.
Adverse effects of shrinkage and moisture
Part G. Mitigating Shrinkage and Moisture-Related Issues
Timber located near heat sources, including flues, boilers, and hot water cylinders, is at a heightened risk of experiencing drying shrinkage. When employing structural softwood for internal applications, it is advisable to ensure that it meets the dry grading standards outlined in BS 4978 (which includes BS EN 518) or BS EN 519. Additionally, such timber should be marked as ‘DRY’ or ‘KD’ (Kiln-Dried) to signify its moisture content control.
Pasquill’s Role in Advancing Home Construction
Pasquill embraces these new standards, offering solutions that meet these requirements.
Our commitment to quality, safety, and sustainability positions us as a leader in the future of housing construction.
Choose Pasquill for your timber floor joist needs and be part of this new era of construction excellence.
Contact Pasquill Today
For more information on how Pasquill’s timber floor joists meet the latest NHBC standards, contact us; Let’s work together to build safer, more sustainable, and superior homes.