How CAD and Off-Site Manufacturing Will Help Us Achieve Our Housing Targets
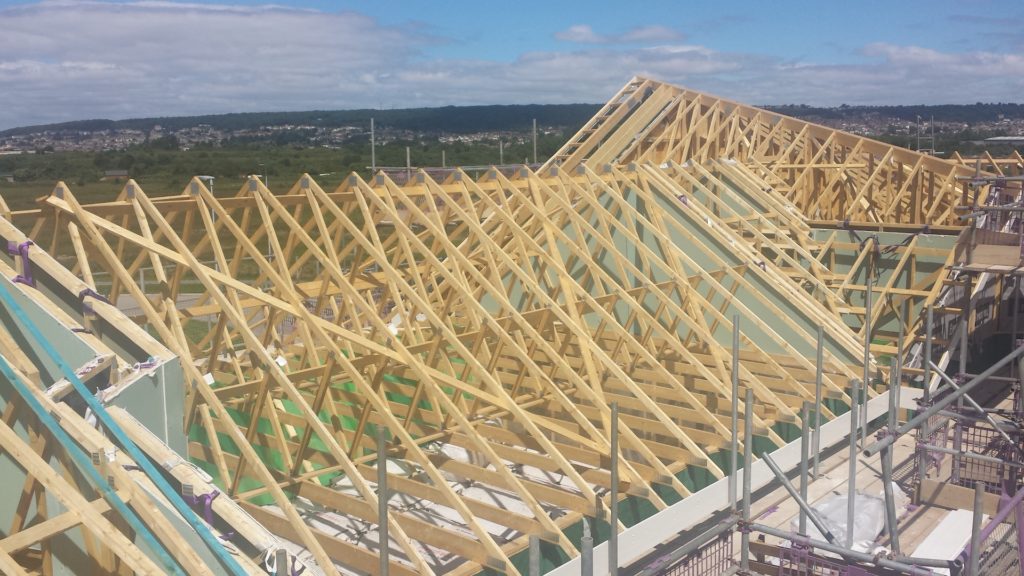
As the UK government’s commitment to build 300,000 new homes annually progresses, our industry should be adopting modular construction methods to ensure we reduce the time it takes to hit our given target.
We’ve certainly seen off-site and prefabricated manufacturing techniques gain momentum over the last few years. Not only is this more sustainable due to a reduction in waste, but it has been found to minimise inefficiencies and eradicate delays on site. Although off-site manufacturing (OSM) is not necessarily a new concept, it has come a long way, particularly as each element of the process has been refined and enhanced by technology.
The rise of design software has encouraged the construction industry to adopt 3D practices and create interactive models to ensure products are manufactured accurately. Not only have we seen these methods improve cost predictability across the supply chain, but the speed of construction increases and the quality of the final build is far greater.
Although the benefits of OSM have been proven, we also need to consider CAD technologies in order to speed up the build process from the very beginning. This is where early collaboration comes into play. More and more we are receiving requests from clients for drawings far earlier in the build timeline.
By working with our clients at these initial stages, we are able to present 3D designs that allows them to truly visualise any concept and better understand spatial planning. It also allows them to identify and eliminate possible clashes on-site, and be involved in structural analysis and energy calculations with our designers. Finally, CAD generated models also enable accurate cost generation ahead of the build, which is generally much more stable when using OSM.
When it comes to our work, we specialise in OSM timber frame elements, such as roof trusses and floor cassettes. As each of our products is bespoke, we do not offer a standardised BIM catalogue. Instead, we create the final design and package it into our client’s desired format so that it can integrate seamlessly into their central model. By adopting this approach, our client is granted a complete overview of the build project, as well as the autonomy to interrogate items and make alterations as projects progress.
There are further ways that CAD fuels efficiency, particularly when it comes to manufacturing as a lot of machinery now accepts instructions from CAD drawings. This is referred to as Computer Aided Manufacturing (CAM). As an example, we’re able to generate files from design models which dictate how we set up our equipment, such as timber CNC saws, presses or lasers. By using these methods, we’re able to maximise material use, improve accuracy and speed up the manufacturing process. CAD technology also shows us how we can increase the volume of equipment in our lorries, allowing us to transport more, safely. Combined with our enhanced installation plans, we believe Lovell Homes penned it best: “Our products are like building with Lego.”
Overall, it’s fair to say that CAD facilitates better OSM. Alongside the obvious benefits of manufacturing houses in a factory; less exposure to the elements, minimal traffic and cost savings, fewer personnel will be needed on site. Although tradespeople will always be important, the adoption of construction technology highlights the need for more designers and engineers that will continue along this path of safer, more efficient and accurate construction.
CAD and OSM is a proven method that will speed up our nation’s efforts to reach our housing targets. It is far safer, will ensure predictable timelines and costs, and above all else, will provide quality homes for people across the UK.