Pasquill: Continuously Improving
Pasquill have invested over £6.5million in our manufacturing sites and design centres over the last five years. The investments have been in equipment, technology and infrastructure, which is part of our long term strategy to improve operational efficiency, performance, quality and sustainability.
Below we would like to share with you all our investments we have made. So keep reading to find out more.
Bodmin, Cornwall
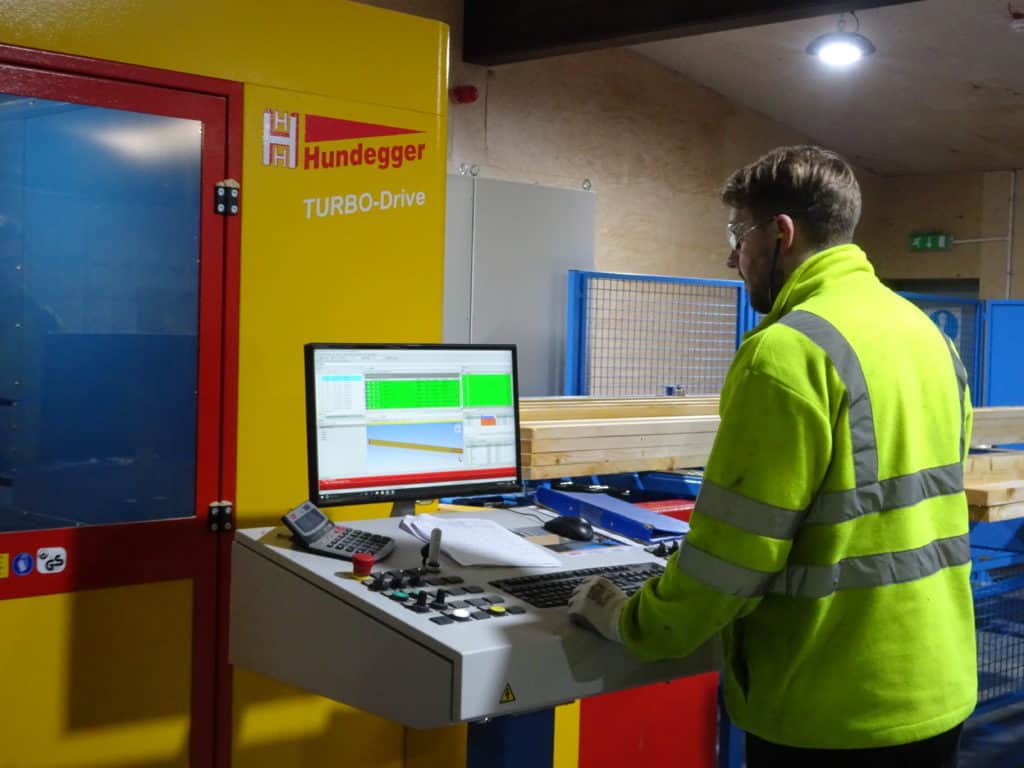
Our site in Bodmin have seen a number of investments and improvements to its site. With the new addition of equipment to the refurbishment of infrastructure.
The introduction of the new Hundegger saw to the site has allowed us to optimise jobs processed which has resulted in precisely cut timber, as well as a reduction in timber waste produced. Additionally, new equipment has been purchased to improve the operational efficiency of the Hundegger saw. A Crossfeed 8500 has improved health and safety for the site, as fork lift trucks are no longer needed to enter the building. The full packs of timber can be easily loaded and returned to storage if required. Furthermore, a conveyor system for the Hundegger saw has improved wood waste removal from the saw and also increases the cutting time on the saw.
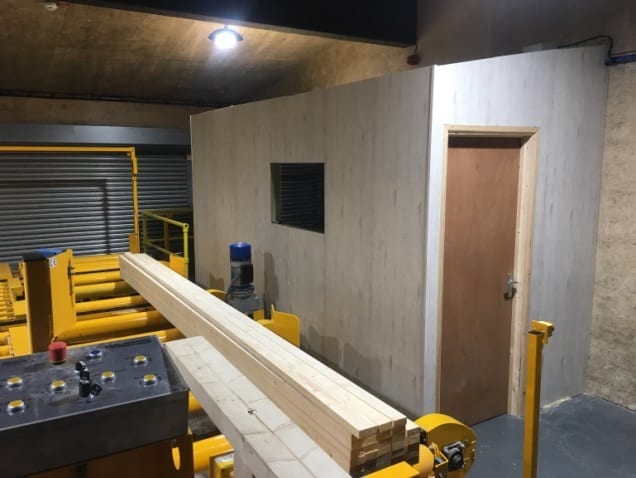
A new optimising room has been created to improve operational efficiency of the jobs run on the Hundegger saw. The new room is now located in the sawmill where all the cut files are now created. This has also improved the way in which Sawyer and Yard Operatives work together, ensuring the correct jobs are received in the correct order.
The site has also had a roof replacement to their Posi building which has benefited the site as more natural light can now come into the building, reducing energy costs in the long run.
ccc
Chorley, Lancashire
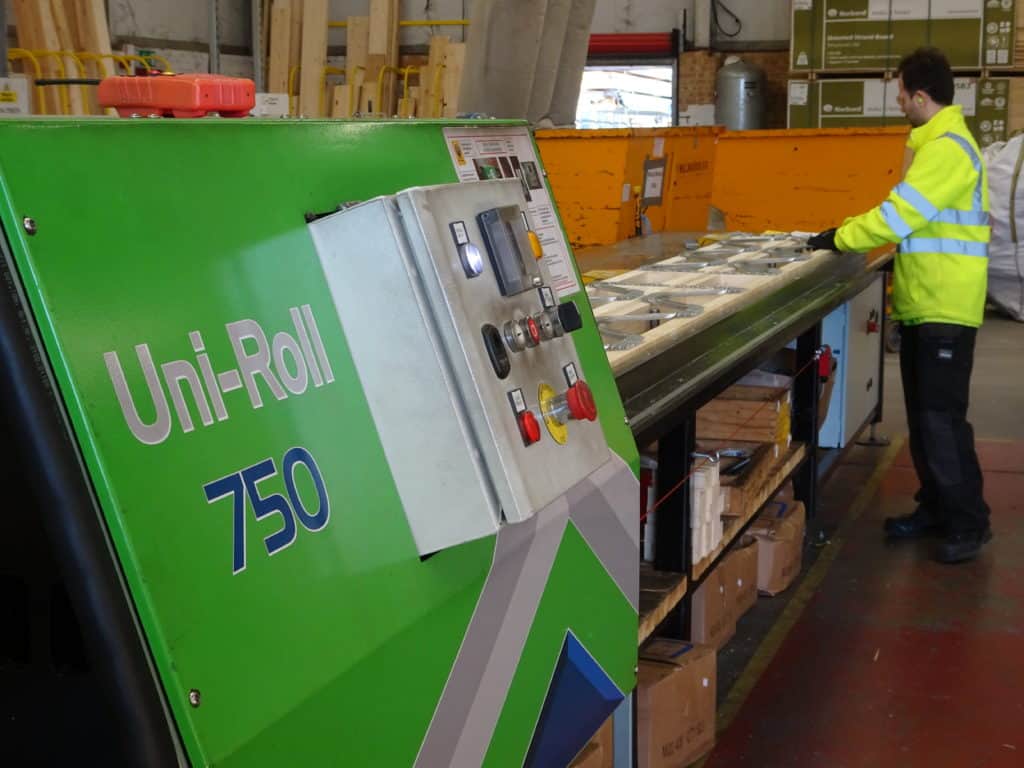
In November 2018, the first phase of the site’s multi-million-pound redevelopment project was approved. This project has entailed a number of investments and improvements to the sites infrastructure and new equipment. Find out more about what is involved in the project here.
Other investments to Chorley we have seen is the introduction of a second Uni-Roll Posi Press machines which has resulted in increase productivity of about 40-50%. The Uni-Roll Posi Press helps improve the overall quality of the product and makes the manufacture of the Posi-Joist more efficient.
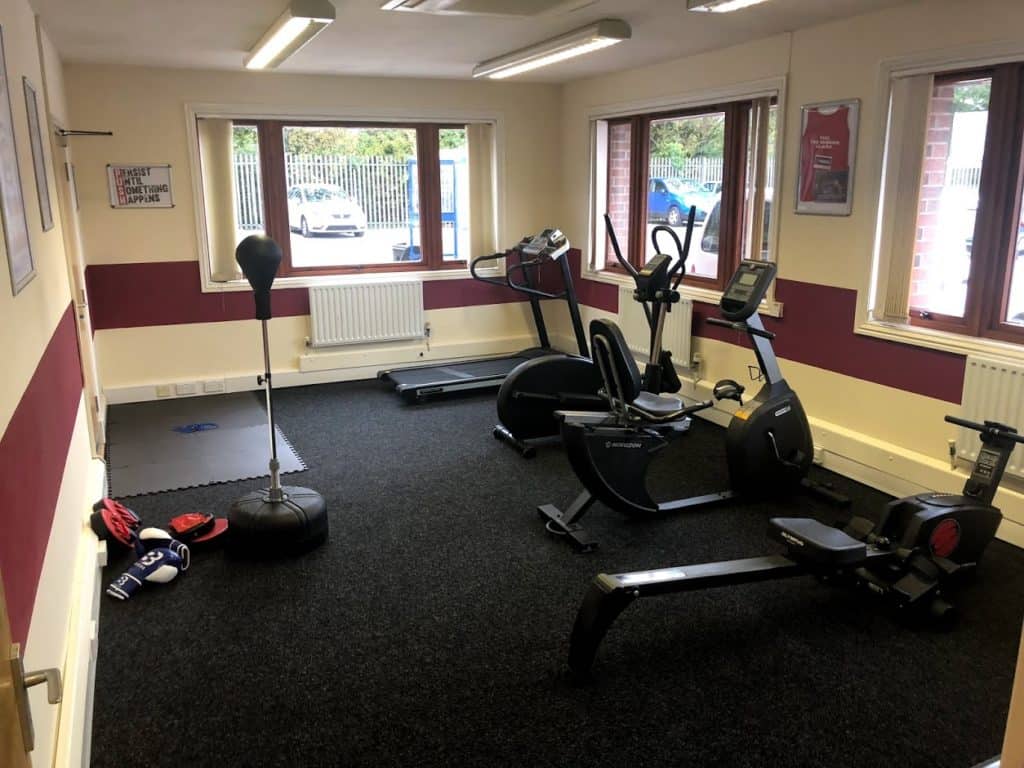
To encourage staff to keep fit and healthy the team at Chorley refurbished an unused office on site into a new gym.
Jon Walsh, Designer at Chorley, commented; “The team needed a place to go to keep fit during their lunch breaks when the weather was unpleasant and as most are parents; family life proves quite difficult in the week to get to the gym and this is where the idea for a gym came about.”
The Gym is open 6am to 10pm, available to all Pasquill colleagues and is fitted out with an exercise bike, cross trainer, a floor exercise area, punch bag, resistance bands, rowing machine, running machine and free weights.
Find out more about ‘The Gym’ here.
Inverness, Scotland
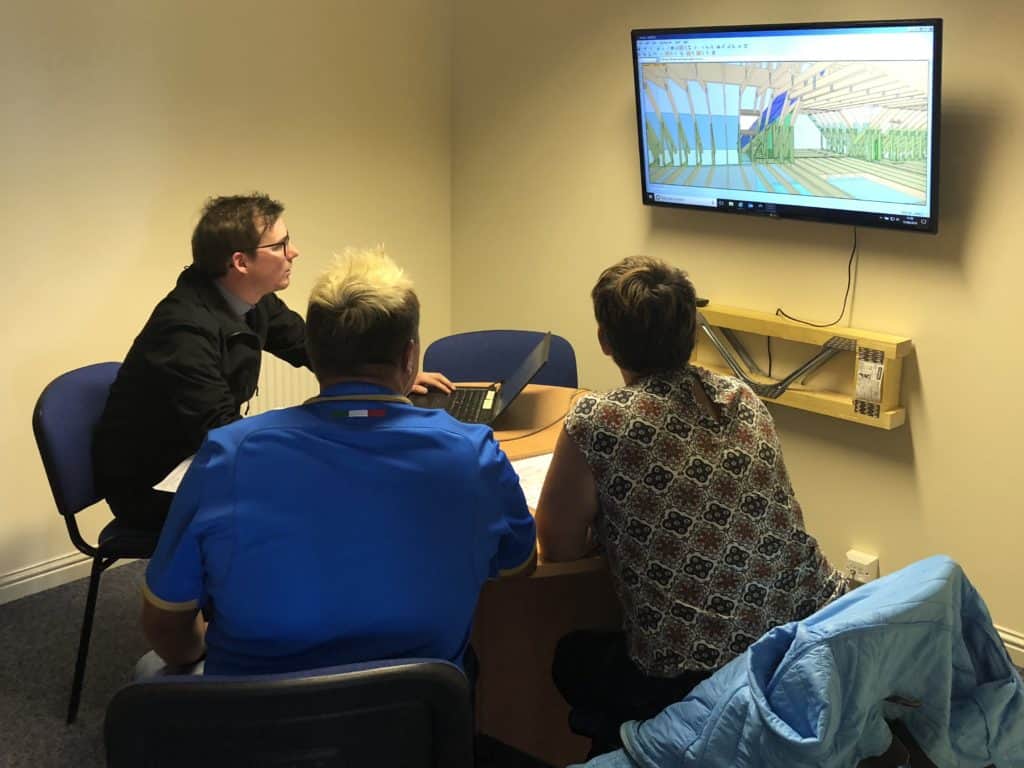
To improve the customer experience of the site’s meeting room, Inverness have created a room that incorporates a more visual and interactive way of viewing and discussing projects with customers. The customer experience meeting room consists of a TV screen which Designers are able to show their projects in 3D and Augmented reality. Find out more about the room here.
ccc
ccc
Newport, Wales
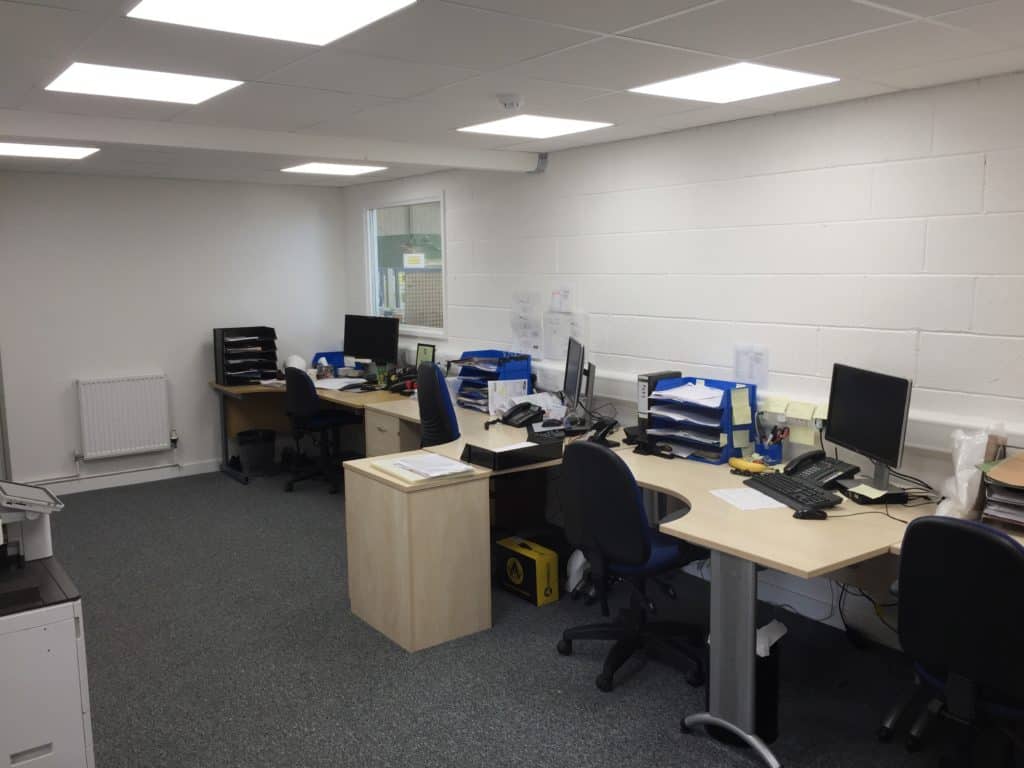
The Newport site has had a refurbishment of their office, kitchen and welfare facilities. The team were working in a cramped and unorganised environment, with not the best facilities. The new refurbishment to the site has now improved working conditions which has improved employee productivity and morale. The site is better equipped and organised which has enhanced their environment to work in.
ccc
ccc
Oldbury, Birmingham
In 2018, our Bromsgrove team relocated to a new office in Oldbury, situated with our sister brand, Minster.
The relocation has many benefits, such as more parking and free parking for both customers and employees, a more spacious office for a team to work in and a large meeting room which is available to discuss customer projects. More information can be found here.
Redhill, Surrey
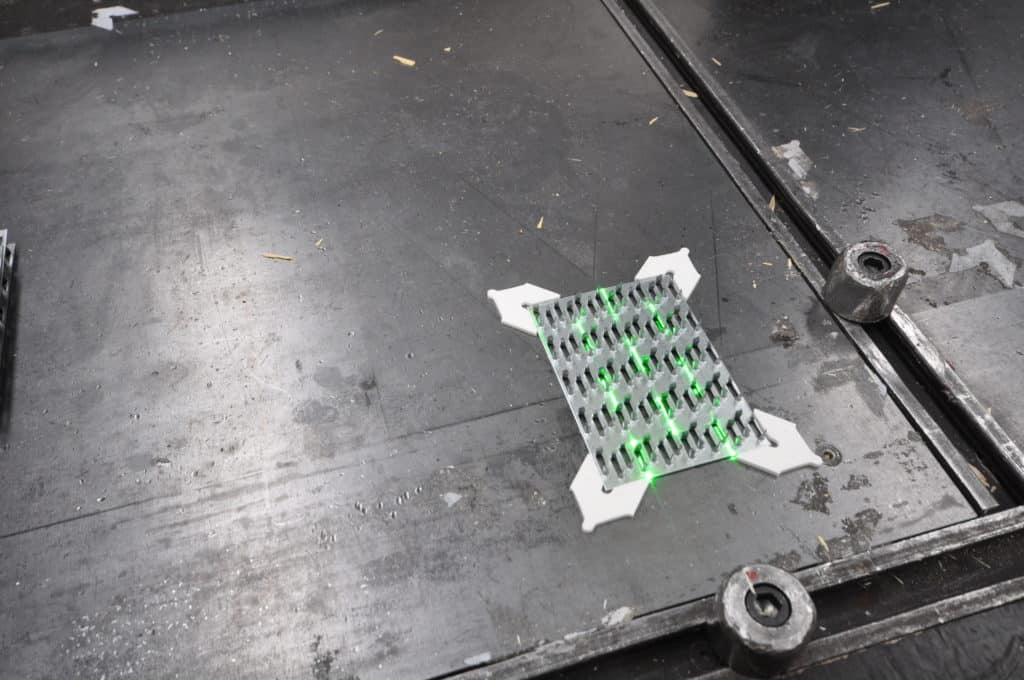
The re-location and installation of new and existing manufacturing equipment has been put in place to increase productivity, maximise workspace and provide a reduction in energy use, at our site in Redhill.
Redhill has also seen the introduction of the Hundegger saw and Crossfeed 8500, which the team have already seen the major benefits from the new equipment.
Furthermore, laser technology has been installed on the roof truss beds to help Operatives place metal plates on the trusses. There are four key benefits to the laser set up technology: firstly, it reduces set up time of the first truss. Secondly, the cycle time of the trusses manufactured is quicker, also the technology allows new Operatives to be trained easier and quicker and finally, the quality and reliability of using the lasers as well as the end product.
Stoney Stanton, Leicestershire
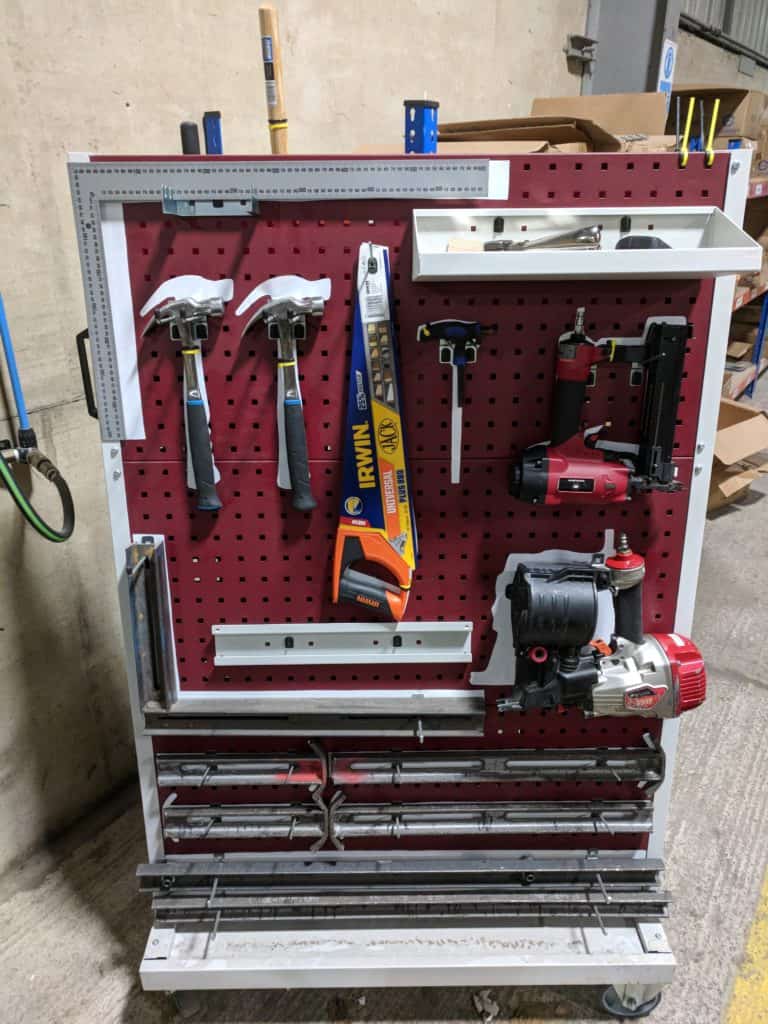
Tool and cleaning stations have been introduced to the site at Stoney Stanton. This has not only improved housekeeping but has a positive impact on some of the eight wastes – reduced walking, looking for tools and the elimination of any slip or trip hazards.
The branch has also taken delivery of a 14 tonne rigid vehicle, which is ideal for delivery where access to customer sites are restricted.
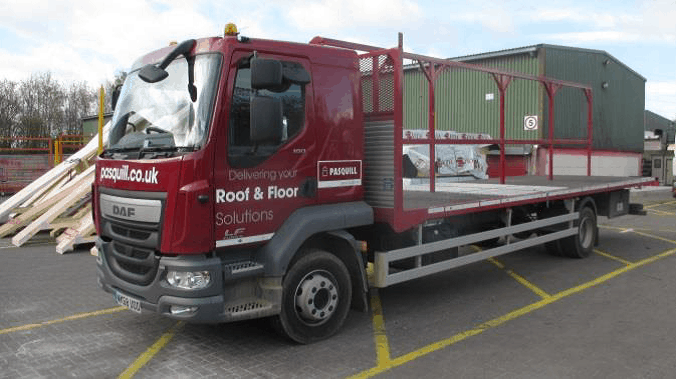
ccc
cccccccccccccccccccc
Uddingston, Scotland
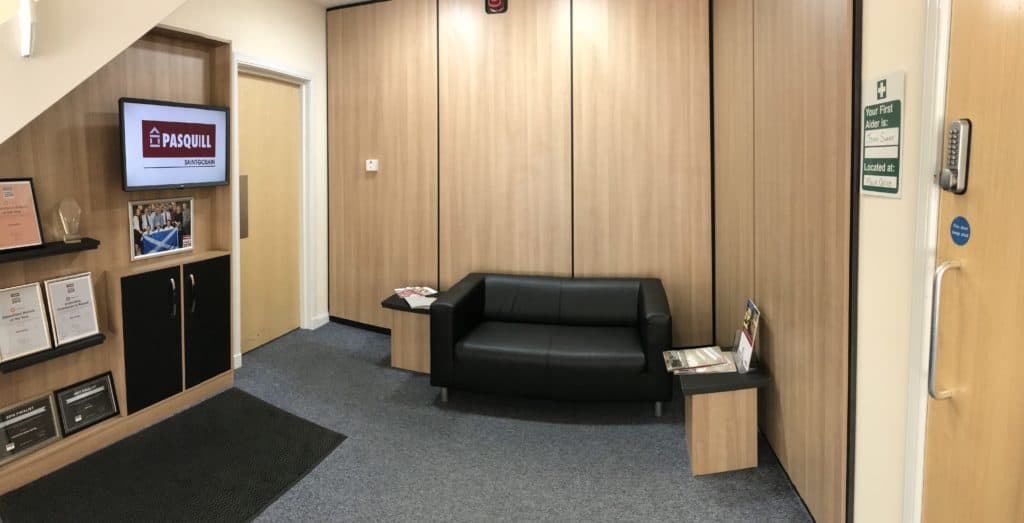
Our team in Uddingston, have spent time improving their customer reception area, which provides a much more relaxed and comfortable environment.
Steven Tracy, Commercial Manager (Southern Scotland), commented, “The new and improved reception area creates a more professional atmosphere from the minute a customer, or employee, walks through the front doors. This not only makes the reception look nicer but also improves our customer’s experience – one of Saint-Gobain’s Attitudes.”
The team have had a number of positive comments and feedback from visitors and customers.
Gabriel Prior, Continuous Improvement Director for the OSS Division, said: “We are continuously investing in all our sites across the UK to ensure they are running efficiently and performing at the cutting edge. These investments will allow us to design and manufacture quality products more efficiently, giving our teams the tools to bring our clients’ visions to life.”