Making on-site safety safer through efficient loading processes
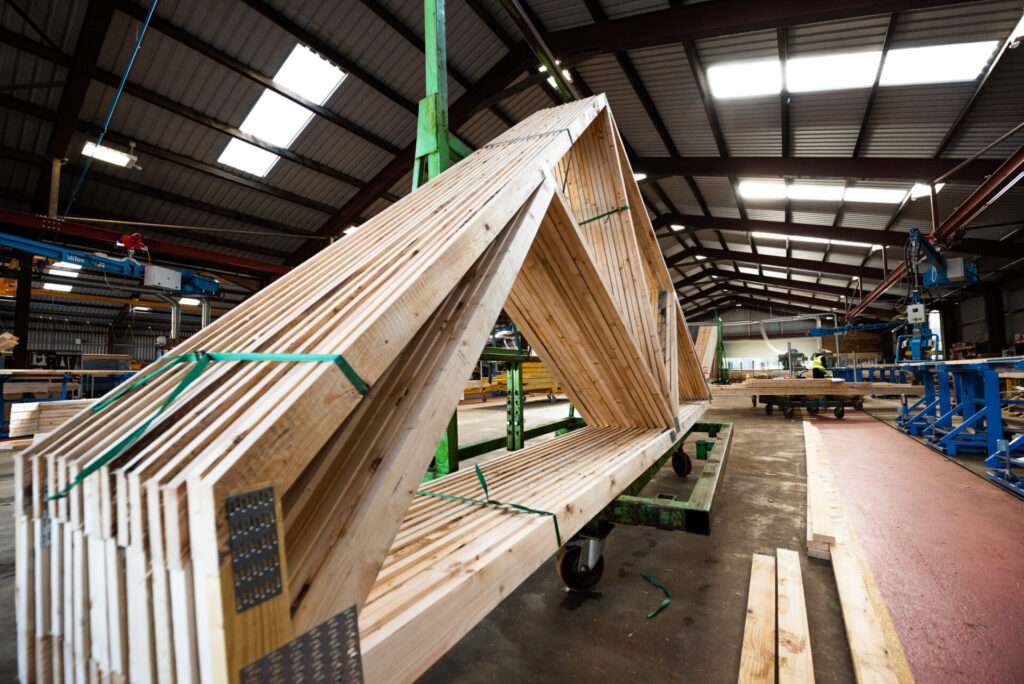
Safety is a top priority in any field, but even more so in the construction industry. Roofing Today reported that in 2023, 20% of working days in construction were lost due to workplace injuries. 14% of these injuries were caused by moving objects and 7% while handling, lifting or carrying.
Pasquill and the wider Saint-Gobain Off-Site Solutions division take colleague wellbeing seriously, and actively work towards ‘Zero Harm’, meaning all colleagues go home safely at the end of each day.
The safety of our colleagues, contractors and anyone who comes into contact with our business is of utmost importance to us, and we are continuously working across all our sites to ensure safe practices are observed.
In this blog, we’ll talk more about how we go the extra mile to ensure everyone stays safe on-site, from detailing our safe and efficient loading processes to our accreditations that prove our commitment to colleague safety.
Efficient loading practices
One of the ways we ensure safety is by implementing efficient loading processes, which can help avoid accidents both on-site and in our factories.
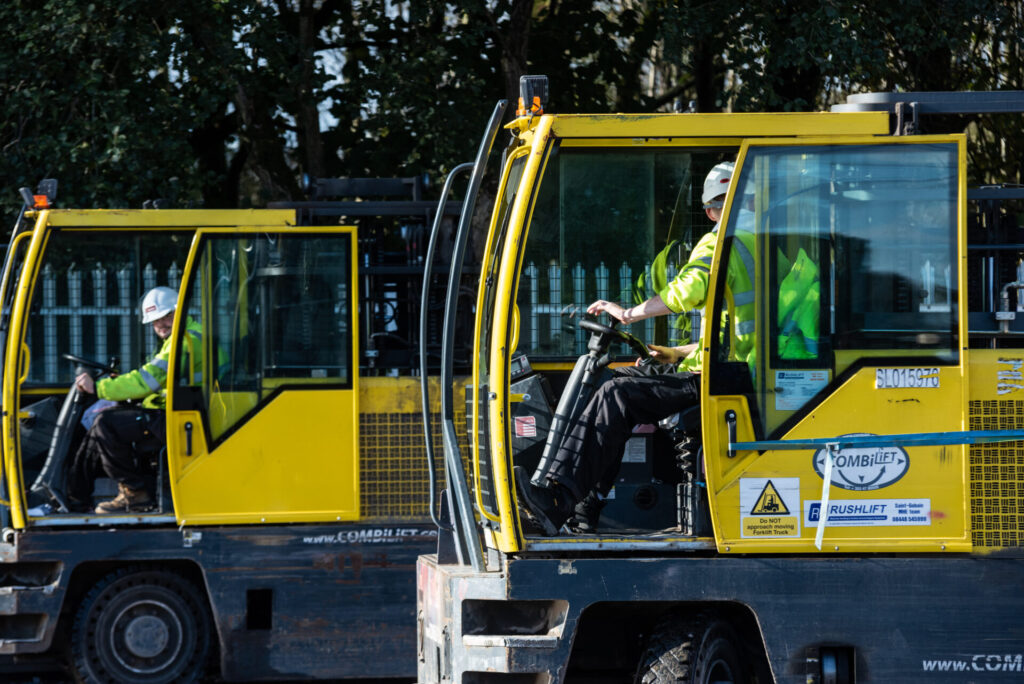
Safe loading
The integrity of the load depends on the vehicle loader (VC), who is responsible for securing heavy goods onto a transport vehicle. The VC must ensure that trusses are firmly tied to the centre bars using blue rope. Only one coloured rope (in this case, blue) is used in the loading process to ensure there is no confusion when it’s cut once the trusses are delivered to the site. The centre bar is a middle support on a trailer bed that loads are secured to, ensuring even weight distribution and preventing the Roof Trusses from shifting during transport.
After loading the trailer and before the vehicle leaves the site, the loader and the delivery driver complete a checklist to ensure offloading will run safely and smoothly on-site. The driver must ensure that trusses have been secured with both a visual and a tug test, and check that the height of the load doesn’t go over the height designated in the pre-delivery load plan.
Before leaving site
To ensure safe spacing, the driver will check the trusses width and overhang. Additionally, they’ll check that the metalwork bags are easy to reach and are secure, as well as ensuring that all crane offloads the purple lifting slings are reachable from ground level. Purple lifting slings, much like the blue ropes used to secure the trusses to the centre bars, are used in conjunction with our transport provider XPO to ensure they are easily and quickly identifiable.
Drivers must perform a snatch test after attaching the unit to the trailer. To do this, ratchet straps are applied securely by the driver on the trusses to ensure there’s no risk of them falling. Drivers must also add any markings or light boards to the back of the trailer or trusses based on how much the trusses overhang.
If a load overhangs the end of the trailer, we will mark it up and make it more visible in the following ways:
- Up to metre overhang – no additional markings required.
- 1-2 metre overhang – markings will be added to make sure the load is more visible to other road users.
- 2-3.05 metre overhang – we will fit lightboards to ensure the end of the load can easily be seen.
- Over 3.05 metre overhang – we will notify the Police for extra instruction.
If the load overhangs the side of the trailer by more than 305mm, then again we will notify the Police.
To ensure the load can safely be transported on the road, and that when it reaches its destination it can be unloaded safely, the driver of the vehicle will complete a visual check. They will consider any potential risks and take preventative measures before leaving the site. Additionally, they will complete a checklist, which will include:
- Checking the vehicle’s condition.
- Ensuring the load is secure.
- Completing a vehicle defect report and load checklist.
- Assessing the load’s measurements and making sure that any metalwork bags and purple straps are reachable from ground level.
- Checking that all the required equipment for offloading i.e. PPE, cutting pole and ratchet straps are available for use once the delivery reaches the site.
In Transit
Once the delivery vehicle leaves site, the driver will stop regularly to make sure the load is still intact, as trusses can move in transport.
Once the delivery arrives to site, the driver will again assess the load to ensure it is safe to unload. The area for unloading will be reviewed to confirm there is enough space for the unloading process to happen safely, without causing harm to anybody who is assisting. The driver will also speak with the site support team who will be unloading the vehicle to make sure they fully understand how to unload the trusses in a safe manner.
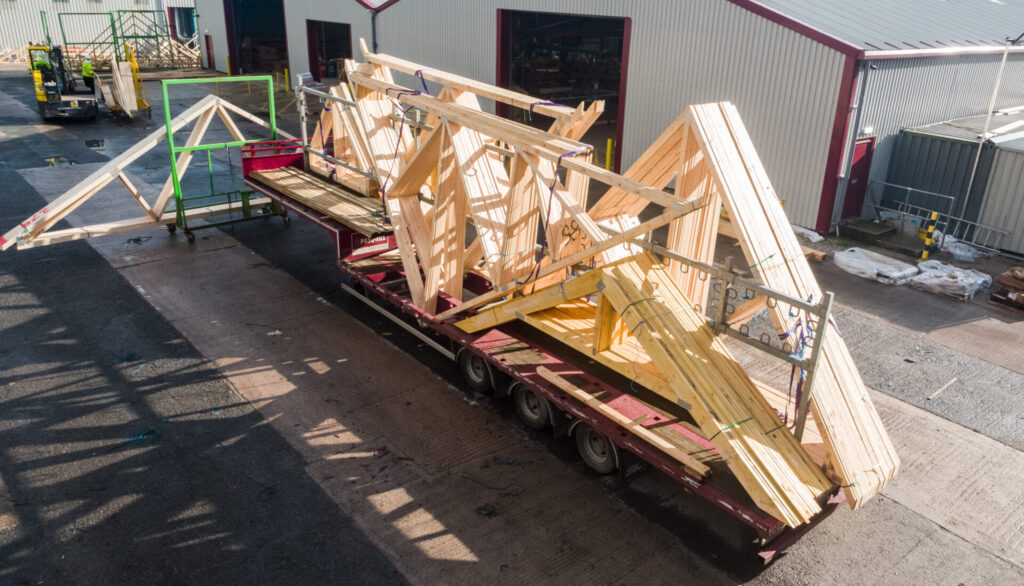
As unloading begins, the weight of the trusses will be managed by cranes or other appropriate mechanical equipment, such as a telehandler or forklift. Once the weight of the truss has been supported by the equipment, the driver can remove the blue rope that is holding each individual truss together.
The trusses will be safely loaded onto the truss rack by crane, and secured to the rack using new blue rope to make sure they don’t fall, protecting both the product and colleagues from harm.
How else do Pasquill work to keep you safe?
We work off-site to make life better on-site
By utilising controlled factory environments to manufacture our products, we are helping further reduce risks on-site. Our trained colleagues use precision machinery to make each component, and once the product arrives on-site, it is craned into place meaning less time is spent working at height.
Technical guidance
An additional way we provide support for safety is through providing comprehensive technical guides that cover a range of products and how they are to be handled safely to prevent injuries. These guides are easily accessible on our website and can be circulated within your teams.
Accreditations
We have a membership with the SAFE contractor scheme that reassures you we are adhering to best practices. The SAFE contractor scheme is a health and safety accreditation scheme demonstrating our commitments to health and safety, sustainability and ESG (Environmental, Social and Governance).
To encompass all aspects of safety, fuel efficiency, vehicle emissions and improved operations, we adhere to the Fleet Operator Recognition Scheme (FORS) voluntary accreditation. FORS covers vehicle and driver management, safety and operations. Having this accreditation helps to elevate our fleet’s standards and make sure you are getting the best quality – service.
Whether in the factory or on-site, the well-being of our colleagues is paramount, and we work hard to enforce regulations and standards to ensure everyone remains safe at work.
Just one example of this is the Dare to Care initiative, which we strictly follow as part of the Saint-Gobain Off-Site Solutions division. Dare to Care promotes safe practices across all our sites and encourages colleagues to speak up if they see someone carrying out a task unsafely. We ask that all colleagues take a personal responsibility for safety on our sites, to reduce risk and improve Health and Safety.
Get in contact today to discuss our offerings and how we can help with your next project: https://pasquill.co.uk/request-a-quote/.
For more information on our loading processes check out our technical guides here: https://pasquill.co.uk/resources/technical-guides/.