Improvements to efficiency and safety at Redhill site
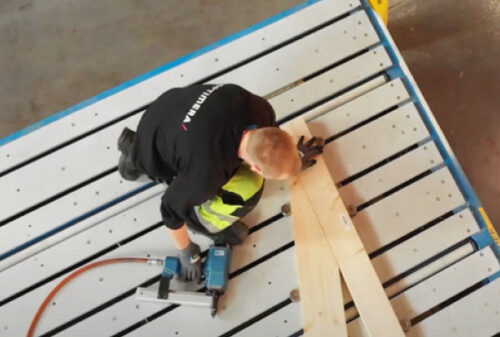
Several recent investments at Redhill have made the site’s operations safer and more efficient, enabling it to provide an improved service to the customer.
With the help of our sister brand Intrastack, we have added a new Swish storage shed to help store our Swish products, worth £8k. These products were originally taking up a large section of the yard and this new storage system frees up space for other work and removes the risks of damage.
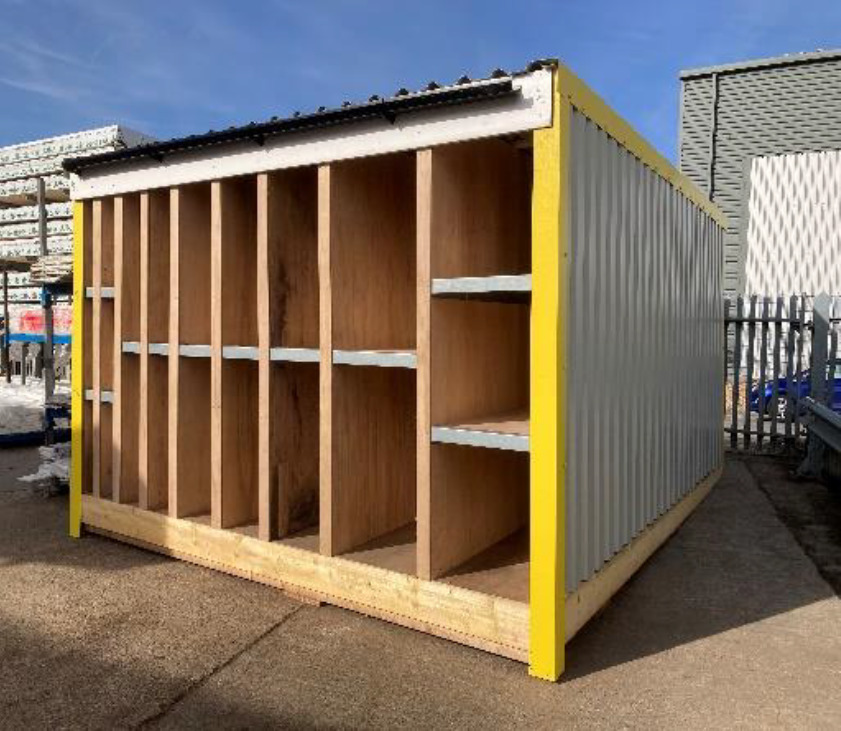
We have also invested £450k into four electric Combilift forklift trucks and one Pedestrian Stacker with a designated electric charging point area. Cost-effective to run, the new lifts require less maintenance and suffer fewer breakdowns while reducing carbon emissions to 0% – enhancing our efficiency and sustainability at the same time.
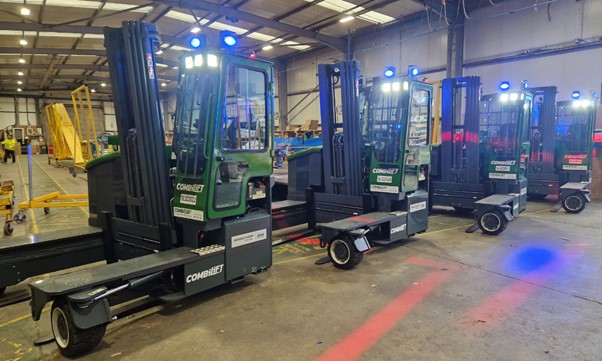
In addition, we’ve been laying the groundwork for the completion of a £6 million investment at Redhill and Stoney Stanton: the Randek Autoeye project, which will be the UK’s first automated truss production line.
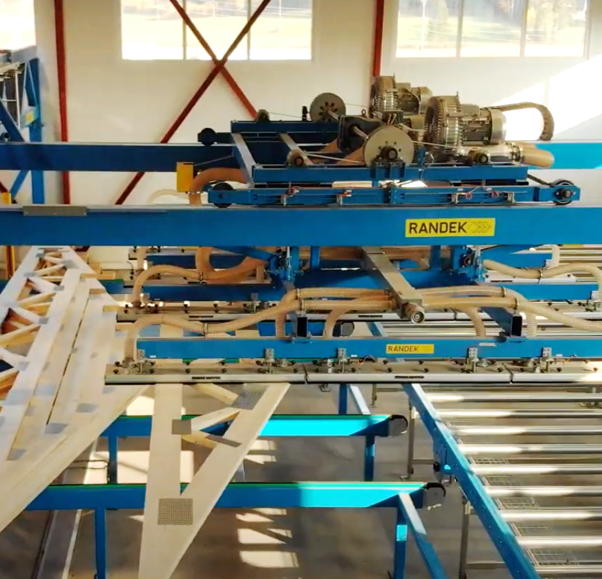
The Randek machinery constitutes a significant and innovative investment that will increase capacity and help to future-proof the business. Helping to fill the off-site and on-site skills gap, this switch to automation will boost efficiency, accuracy, speed, and safety, as well as free up valuable colleague time so it can be reallocated elsewhere in the factory.
Before work could begin for this project, we had to carry out investigations into the foundation and drainage system and complete boreholes to confirm ground conditions. Additional preparations included a complete re-wiring to utilise electrical capabilities at the site to accommodate the new system.
Finally, due to a TF4 where a JJI pack collapsed by the JJI line, we’ve revised the system by adding supportive pedals to greatly decrease the risk of this happening again.
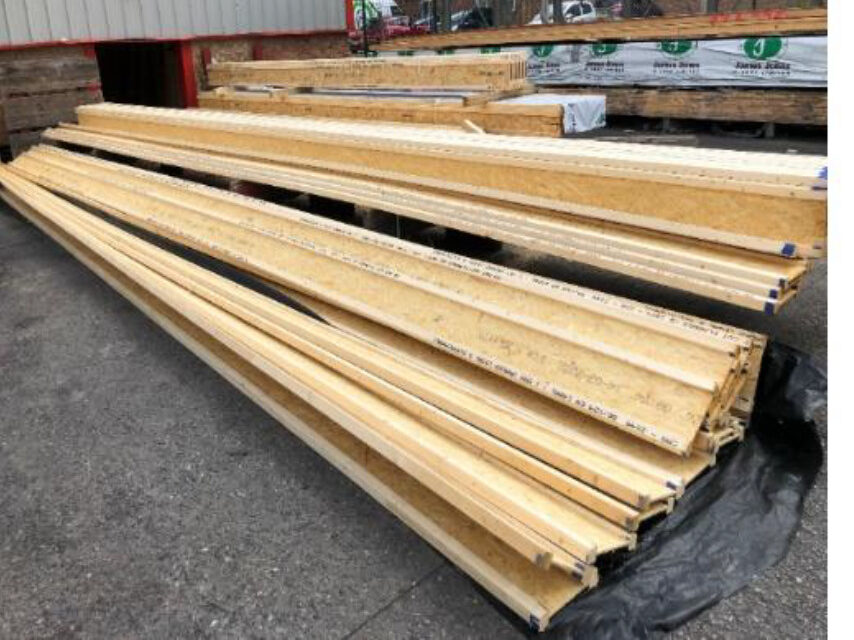
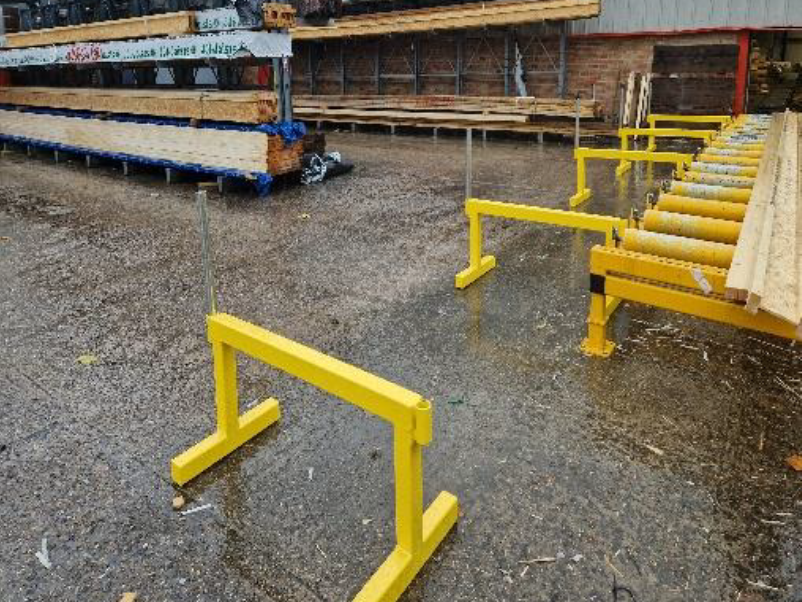
Justas Povilaitis, Site Operations Manager, comments: “The recent investments at our site have all led to significant improvements. Together they have enhanced not only the quality of our products but also the safety and efficiency of our operations. This creates a better work environment and a happier workforce – and ultimately a better service for our customers.”
Our ongoing continuous investment programme is taking place across three years, totals £14.1 million, and also includes providing all sites with an improved puck design that will reduce setting time as well as updated 5S equipment to ensure an organised and efficient work area. To discover the full investments across all our sites, view our full investment piece: https://pasquill.co.uk/pasquill-reveals-14million-investment-programme/.